Auslegung
Ziel ist es, einen Makita-kompatiblem Werkzeugakku zu bauen, der handlich ist und eine hohe Kapazität hat. Da die Werkzeuge annähernd 1000W vom Akku abverlangen, braucht es hochstomige Zellen.
Ich habe das Tool Battery Pack Designer benutzt um meine Zellauslegung zu planen. Wichtig ist, dass das Pack viel Strom abgeben kann um auch in leistungshungrigen Werkzeugen eingesetzt werden zu können. Damit sind mit folgende Möglichkeiten vorgeschlagen worden:
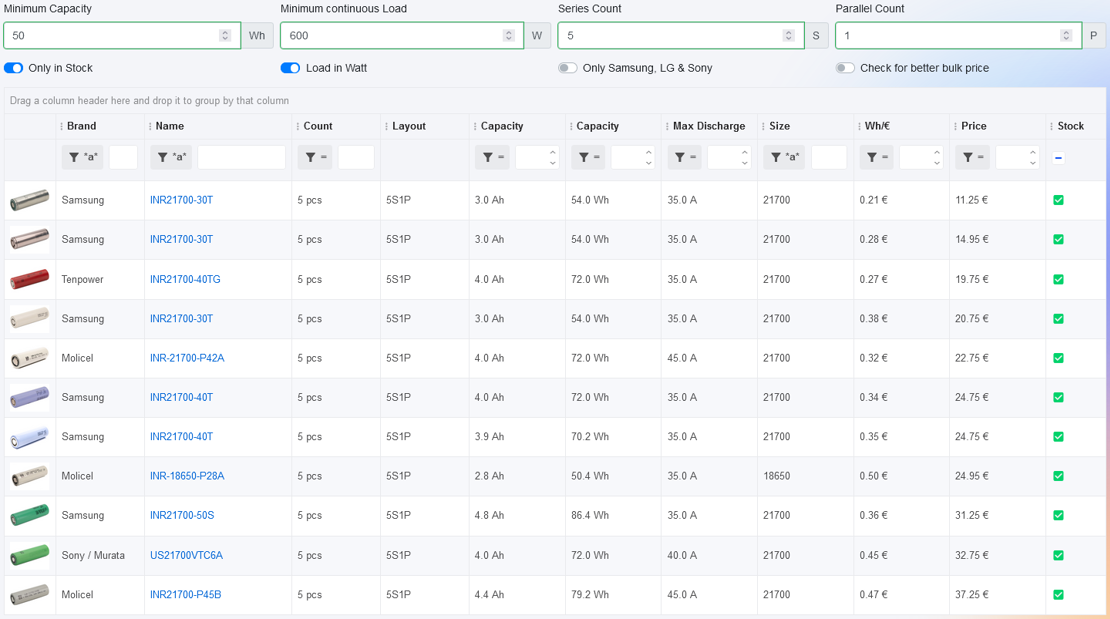
Für die finale Entscheidung habe ich die hervorragenden Tests von lygte-info.dk zurate gezogen um dann die tatsächliche Performance der Zellen herauszufinden. Dabei habe ich mich für die Zelle INR21700-P42A von Molicel entschieden. Diese trifft die optimale Waage aus den drei wichtigsten Parametern: Preis, Kapazität, Leistung.
Ein Auszug aus dem Testbericht:
Hier kann man ablesen, dass die Kapazität unter hoher Dauerlast (30A) bei ca. 3.7Ah liegt:
-Capacity_1110.png)
bei 20A Belastung:
bei 30A Belastung:
-Temp-20.0_1110.png)
-Temp-30.0_1110.png)
Technische Daten der Zellen
Nennspannung: 3,6 V
Kapazität (laut Datenblatt): 4,2 Ah
Kapazität (Hochstrom, 30 A, getestet): 3,7 Ah
max. Entladestrom (konstant): 45 A (laut Datenblatt - mit Temperaturüberwachung)
max. Entladestrom (konstant, getestet, bis 50°C Temperaturanstieg): 20 A
Das heißt nun für das Pack:
5x INR21700-P42A in Reihe für folgende Specs laut Datenblatt:
Nennspannung: 18 V
Kapazität: 4,2 Ah (75 Wh)
Max. Leistung: 45 A (810 W)
Diese Leistung sollte sogar für den Winkelschleifer reichen.
Hier einige Bilder von dem Bau:
Das sind die 5 Zellen, die in dem Akku zum Einsatz kommen sollen:
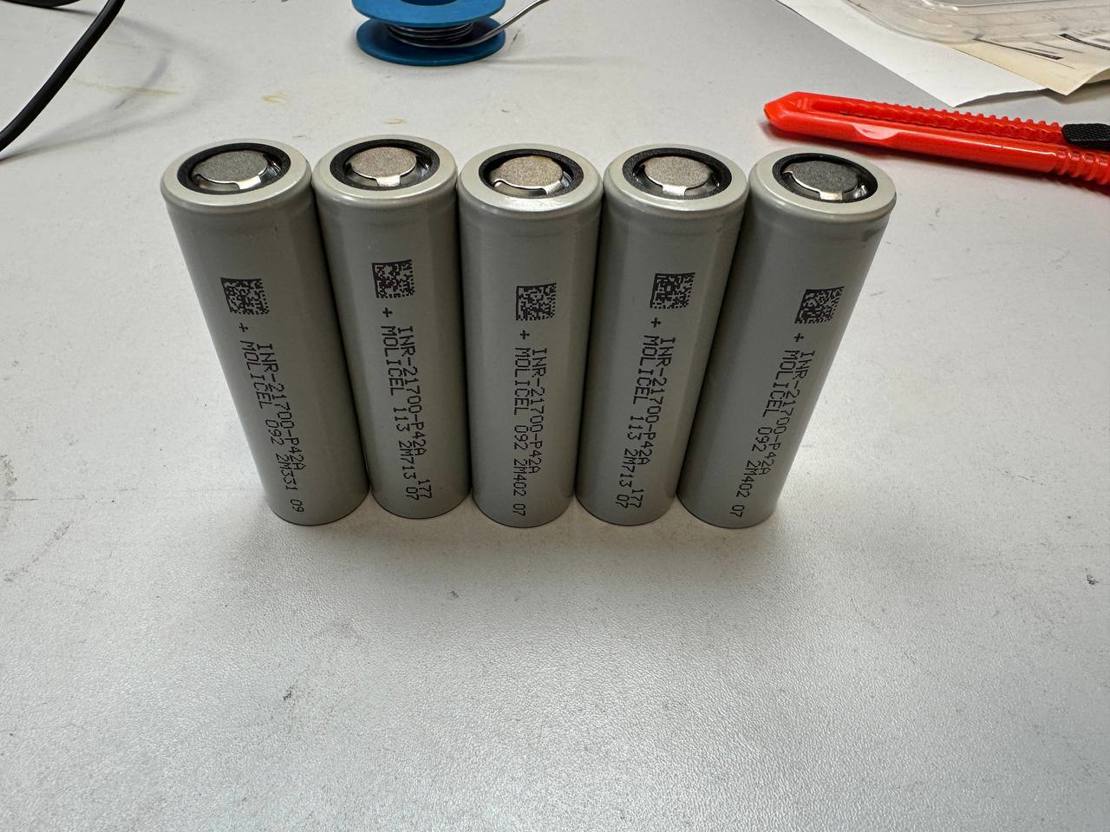
Die Zellen müssen mit Isolationsringen auf dem Pluspol beklebt werden um einen Kurzschluss zu vermeiden. Die gesamte Hülle ist der Minuspol und wird nur von einer dünnen Lage Schrupfschlauch isoliert.

Hier sieht man das vollständige Set. Das Polycarbonatgehäuse, das Batteriemanagementsystem (BMS), Abstandshalter für die Akkus und die Nickel-Leiter, die an die Pole der Akkus geschweißt werden:
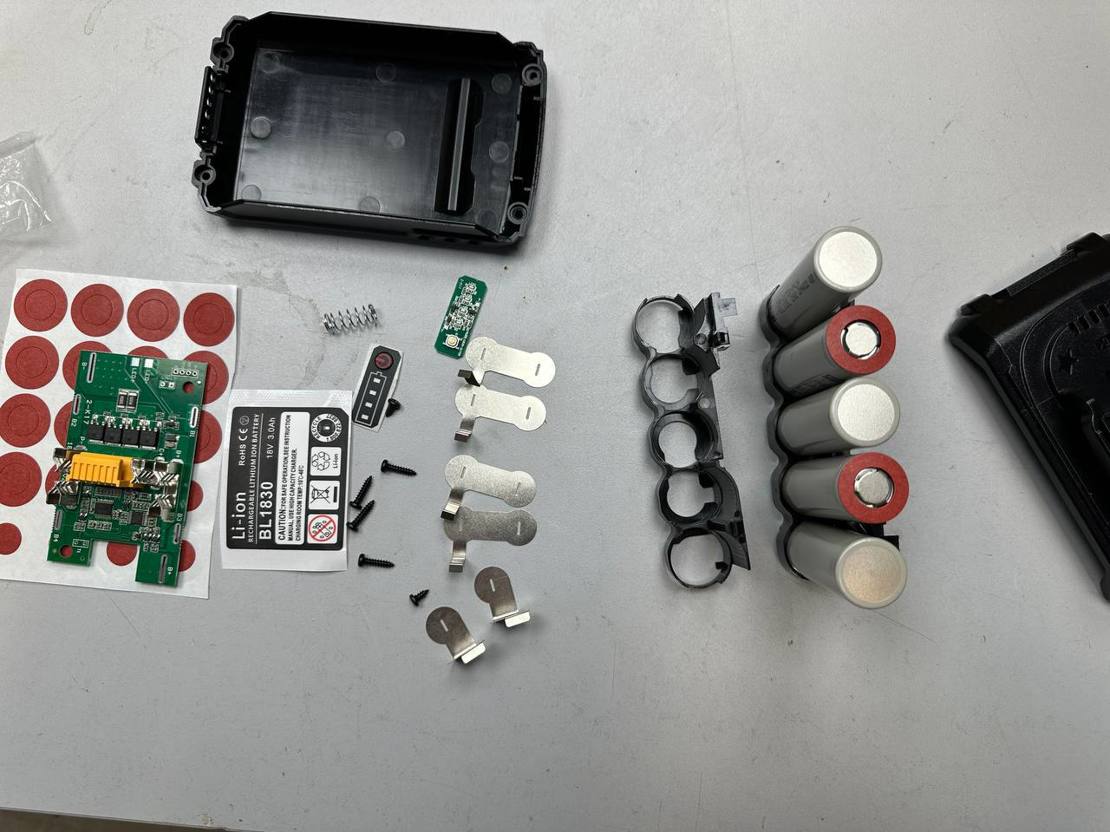
Nachdem die Zellen ausgerichtet wurden, kann nun das Schweißgerät Kweld in Kombination mit einem Superkondensator verwendet werden um die Verbindungsleiter mit den Akkus zu verbinden.
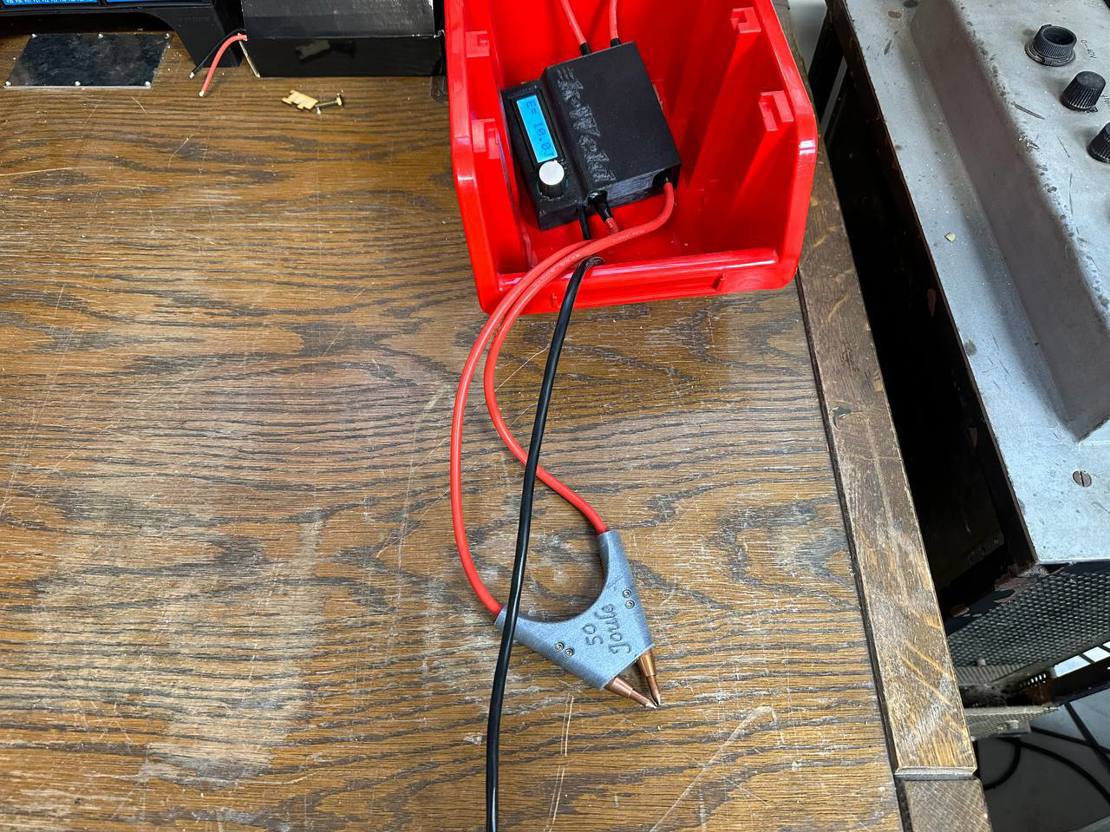
Jeder Pol wurde mit sechs Schweißpunkten versehen.
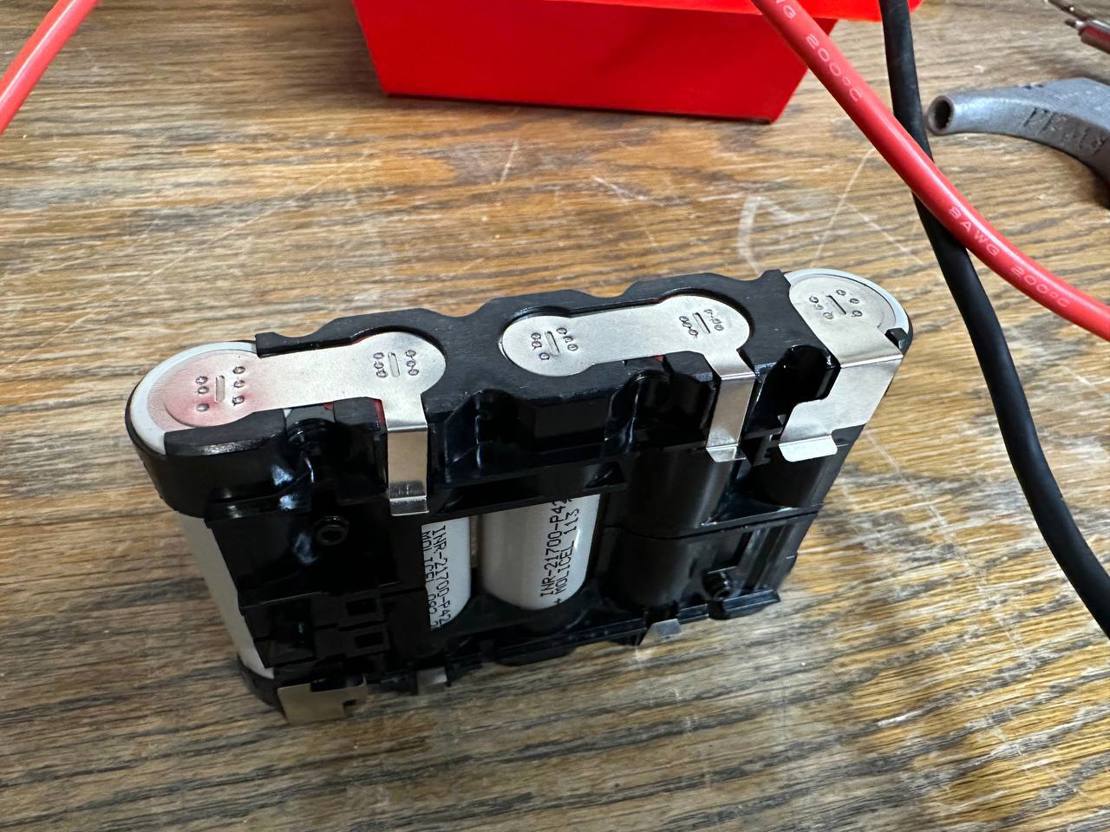
Nun kann das BMS aufgelegt und verlötet werden.
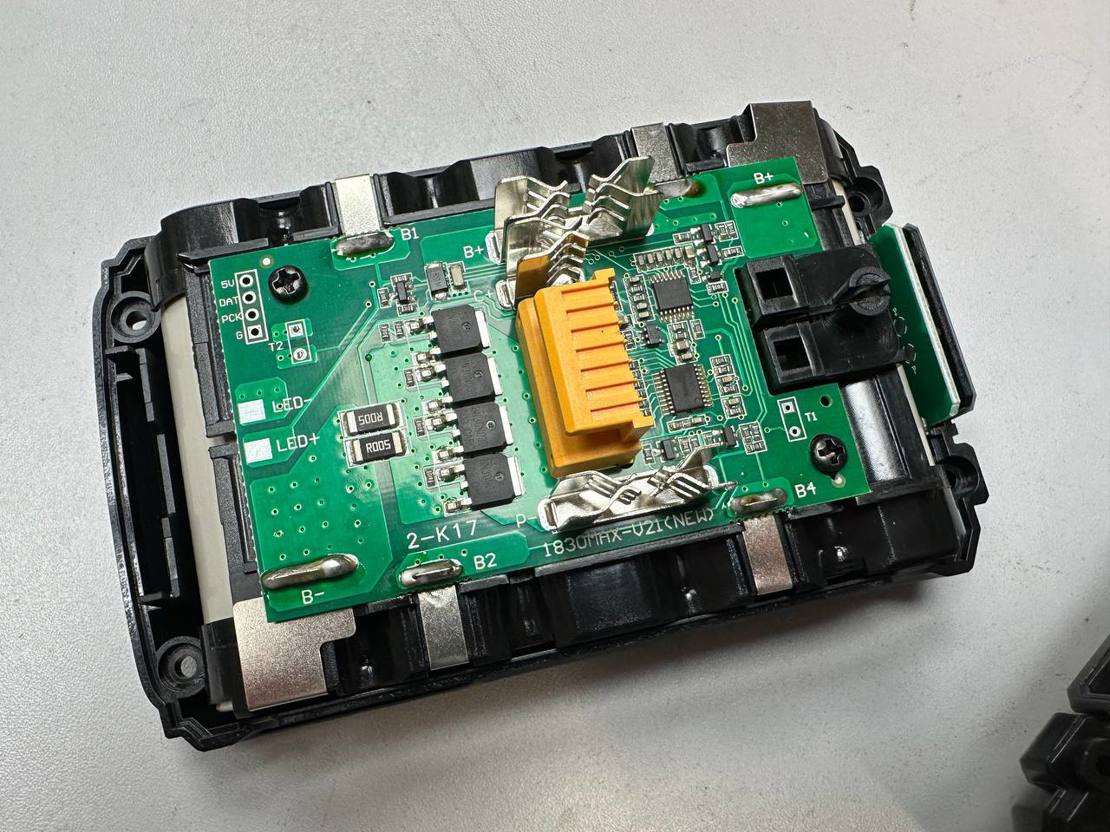
Als letzter Schritt in der Elektronik wird noch der Füllstandsindikator verlötet.
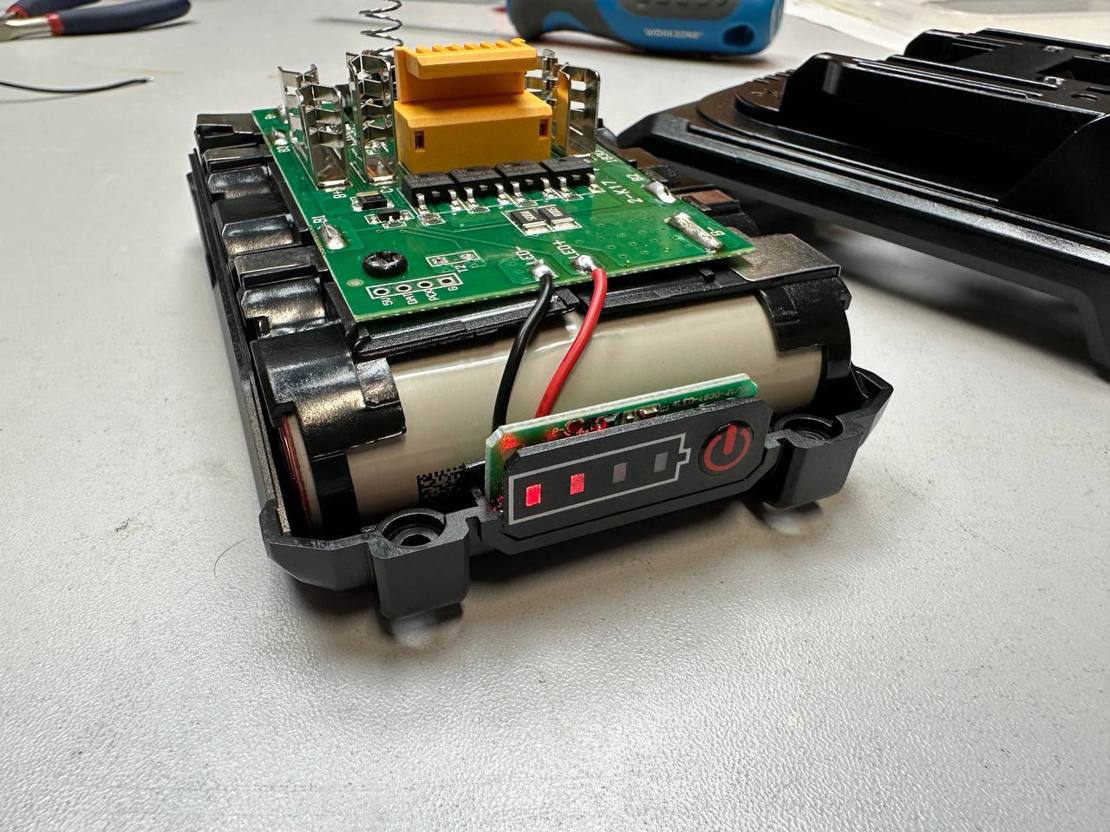
Jetzt muss nur noch das Polycarbonatgehäuse verschraubt werden und fertig ist der Akku!
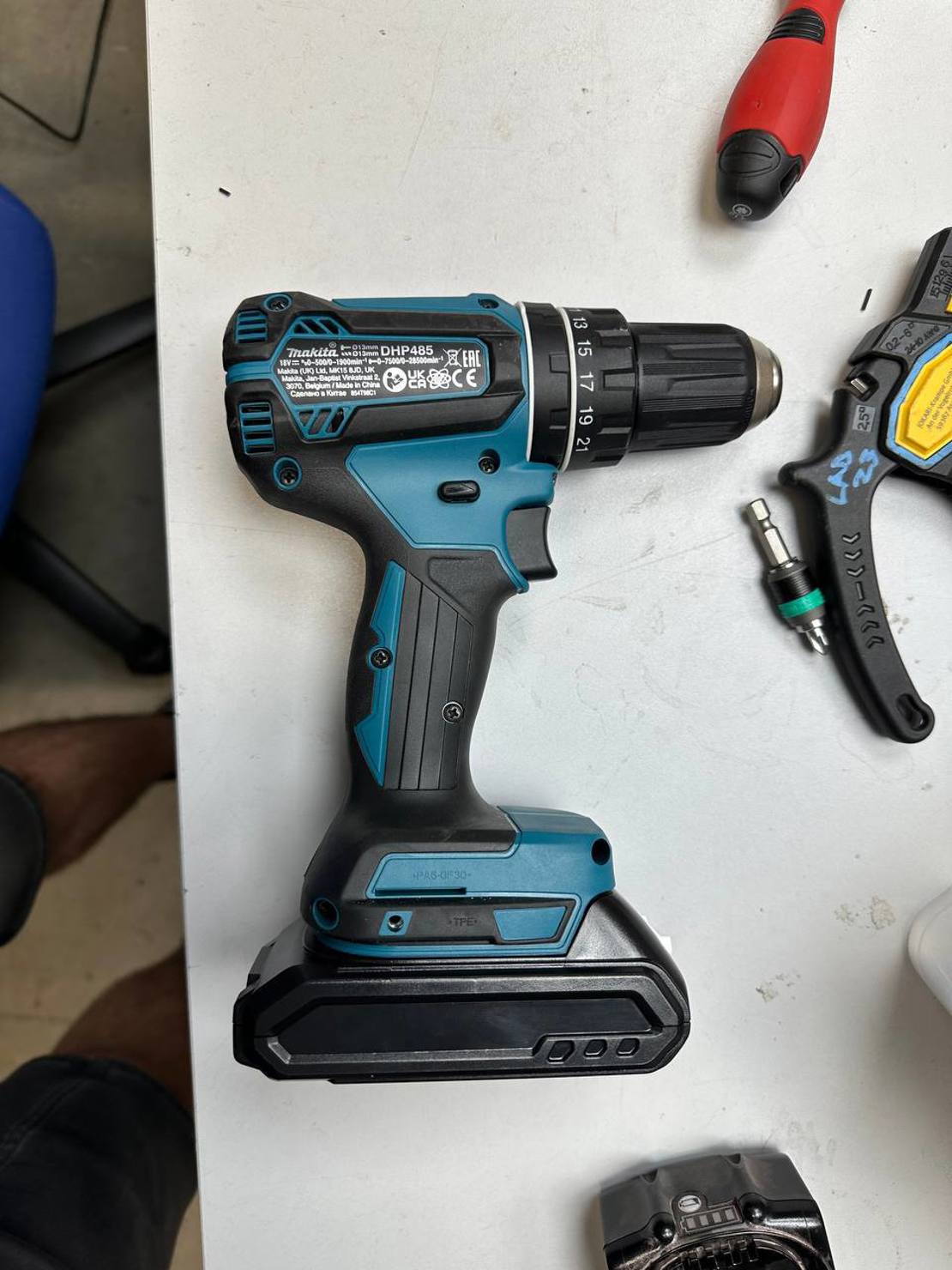